Retrofit for the Future project, Balham
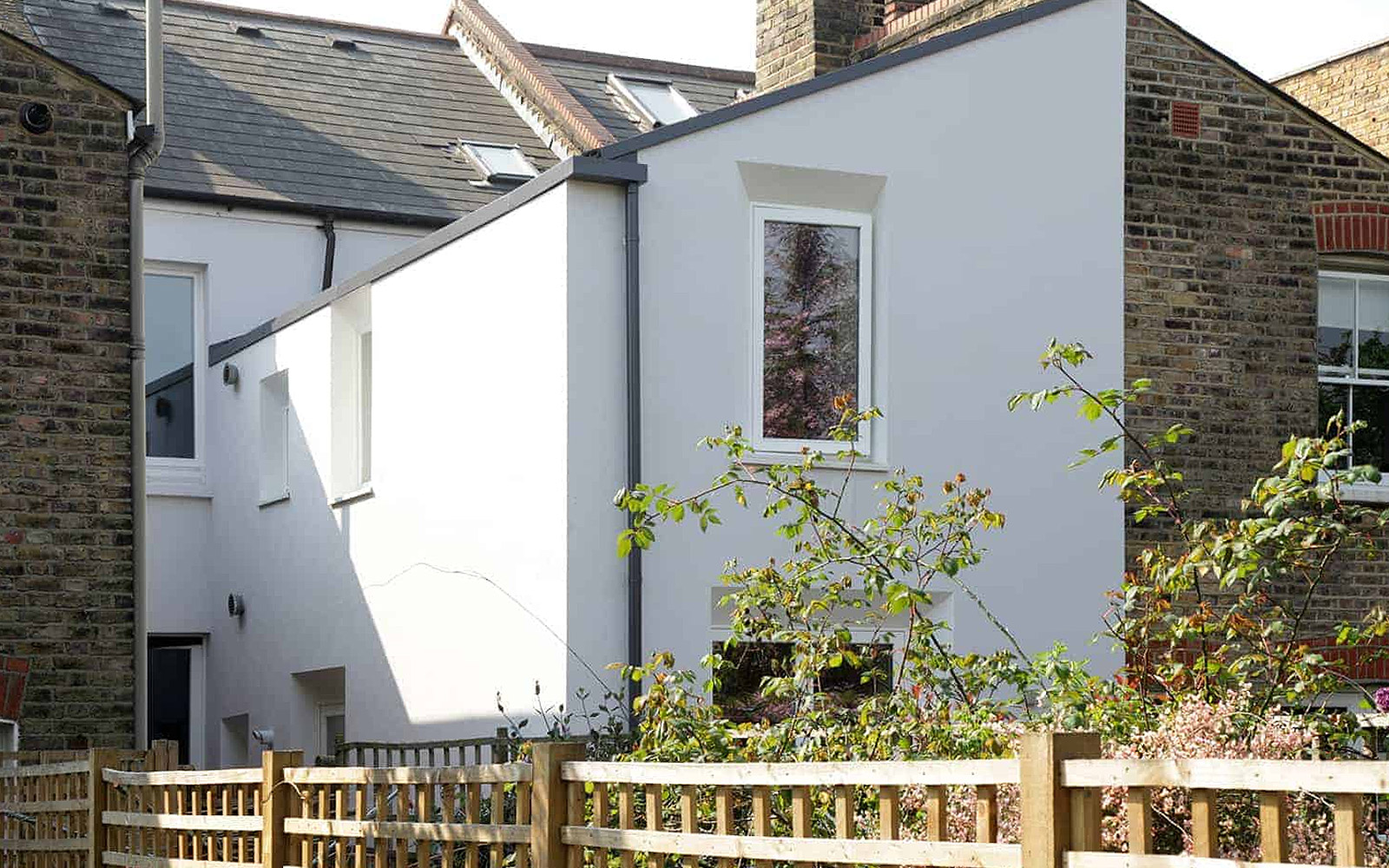
Robert Prewett, Director at Prewett Bizley Architects, recently completed a ‘Retrofit for the Future’ funded project in Balham, south-east London, refurbishing a terraced Edwardian home, to near Passivhaus standards. The house was a 100-year-old, three-bed, solid-walled housing association property.
The project has achieved impressive energy savings, with a space heating requirement of just over 25 kWh/m2/year. To achieve this, the house had to be highly insulated and airtight; the team has managed to achieve an airtightness figure of 1.2 m3/hr/m2 – that’s over 8 times better than the Building Regulations demand for new build.
The project used a combination of internal insulation to the front of the building to avoid impinging on the attractive and well-built streetscape, with external insulation to the rear of the building, where maintaining the pre-existing external appearance of the property was less of an issue. The internal dimensions of the rooms within the rear part of the house were also much tighter than at the front, so taking any space away for insulation would have affected the usability of those spaces. The use of external render at the rear of the building was not without its challenges however and the design team had to develop innovative solutions for relocating the soil stack on the rear elevation and also how to seal the external insulation at the top of the wall (developing a super wide rainwater gutter) to avoid having to replace the roof.
MVHR ventilation
Rob Prewett
High performance timber windows
At the front of the house, double-glazed replica sliding sash windows were specified, to fit in with the nearby conservation area. However 21 Degrees Ecopassiv (since superseded by ULTRA range) high performance triple glazed windows were specified for the rear elevation of the property. In addition, two PERFORMANCE triple glazed outward opening windows (whole window U value = 0.9 W/m2K) from 21 Degrees were also specified.
Rob Prewett
The triple glazed windows have been installed within plywood box linings that were fitted within the structural openings, offering a number of advantages during construction. The relationship between the window and the insulation was also considered.
In line with Passivhaus detailing, the design team lapped the insulation over the timber frame of the triple glazed windows to minimise thermal bridging, but also splayed the reveal to maximise daylight and sightlines.
More information
Passivhaus Refurb Diaries – Rob Prewett’s regular blogs during the refurbishment process
Project details
Architect
Completed
February 2011