Oxford EnerPHit Plus
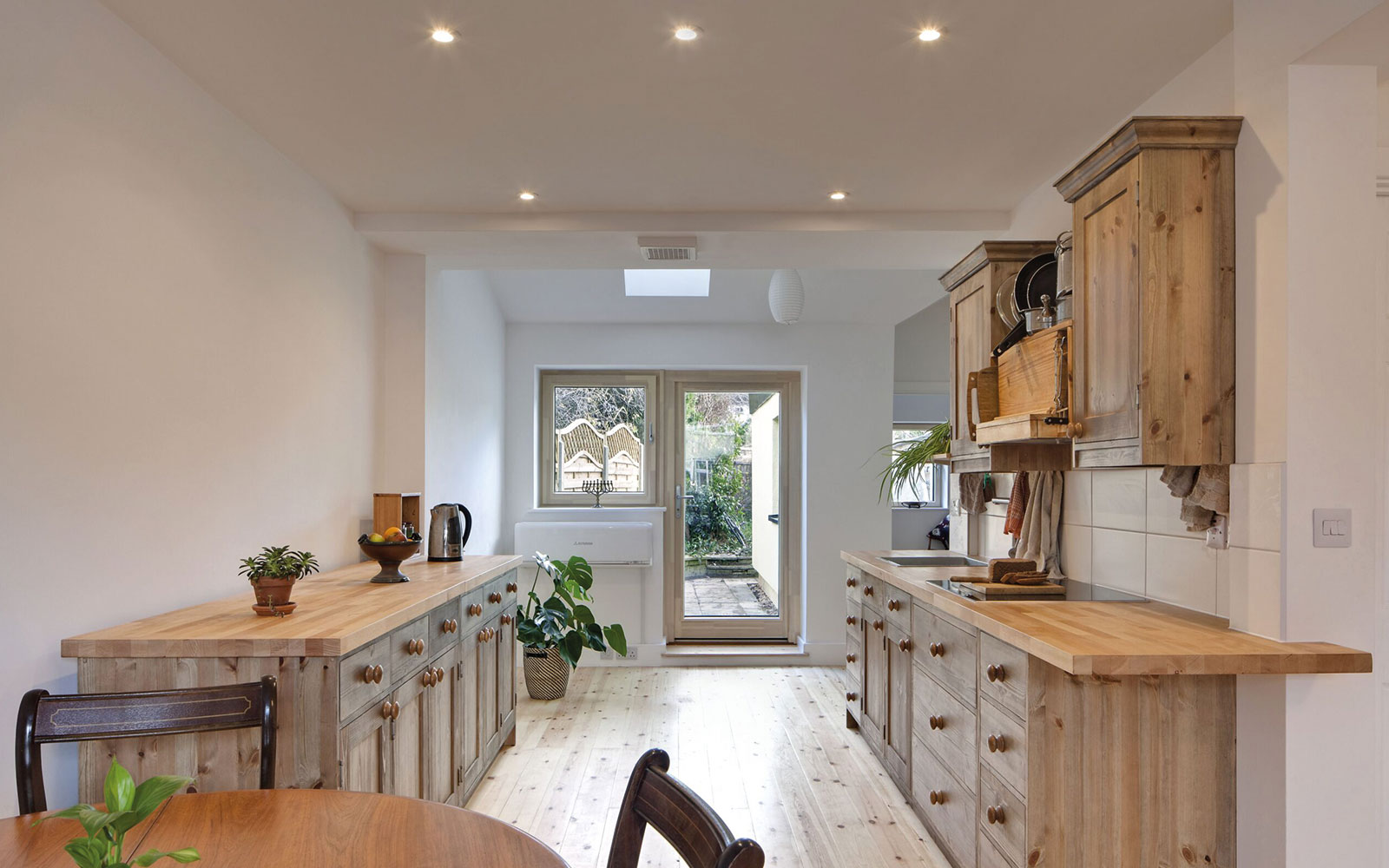
The radical retrofit of an Oxford 1930s semi-detached house has recently been completed and is among the first EnerPHit Plus projects in the UK. EnerPHit Plus has renewable energy requirements in addition to the building fabric requirements of the classic EnerPHit (Passivhaus retrofit) standard. The project was inspired by the client’s desire to radically reduce carbon emissions of the house in line with a 1.5 degree global warming limit by making the home net-zero for energy.
Eco Design Consultants were the architects from the project inception to technical design and Oxford-based architects Transition By Design were the architects and project managers from the tender period through to completion. AMC Build, which had previous experience working on energy efficient retrofits, were the builders on the project. Client Laurie Michaelis has a background in physics and so was able to undertake some of the structural and thermal bridge modelling calculations himself.
The project has achieved its EnerPHit Plus certification in December 2020, with WARM as certifiers.
21°’s PROGRESSION windows, ULTRA doors and MVHR systems were chosen for the project.
Design
Eco Design Consultants modelled the 1938 solid-brick semi-detached house with extension in Passivhaus Planning Package (PHPP) and offered Laurie a number of options, ranging from full Passivhaus standard to AECB building standard. Laurie decided to go for somewhere between EnerPHit and Passivhaus. The PHPP modelling proved to be a useful decision-making tool for making key decisions on the retrofit.
The EnerPHit Plus standard requires heating energy below 25kWh/m2.y and air leakage below 1.0 air change per hour at 50Pa.
Final Airtightness test result: 0.73 air changes/Hr at 50 Pa.
Space heating need: 23.6 KWh/m2/annum
Key elements:
Airtightness measures
The exceptional airtightness levels at the project were achieved by measures such as: designing out problem areas such as loft hatches and chimneys; removing the stairs to plaster for airtightness and then reinstalling; early blower door testing; a skillful contractor and careful attention during site visits.
Walls (main house)
The walls of the main house are solid brick. The roof of the existing house had 200mm eaves, which meant up to 200mm phenolic foam insulation board (with a thermal conductivity of 0.020 W/mK) could be added externally. EWI at a depth of 100mm was also applied to the neighbours’ walls, which means the step at the party wall is less obvious and visible. Extending the EWI across to the neighbours’ house also eliminates the thermal bridge at the party wall between the houses. Solid XPS (extruded polystyrene) was applied right down to the foundations to reduce thermal bridging at the ground to wall junctions.
U value: Under 0.1 W/m2K
Walls (extension)
The single storey extension was build in 1999 with insulated cavity blockwork walls. Where possible, external insulation was used but some of the walls are at the property boundary so internal insulation was necessary. In these cases, the inner blockwork leaf was removed and the new wall made up as follows:
- Original blockwork exterior leaf
- 50mm DriTherm 32 Mineral wool
- 140mm phenolic foam insulation board (under 0.020 W/mK)
- 89mm Dritherm 32 mineral wool in between timber stud
- Plasterboard
U-Value: 0.09 W/m2K
Roof (main house)
The roof was re-tiled and a windtight membrane was installed under the tiles to prevent air and wind movement in the ‘cold roof’ loft space. 600mm mineral wool insulation was added to the loft. Careful attention was paid to insulate the area with sloping eaves (skeeling) and to reduce thermal bridging at the wall and roof junction. The skeeling was insulated with phenolic foam insulation board between the rafters and internally on the sloping ceiling 140mm of phenolic foam insulation board was applied. Solar PV panels were embedded in the roof tiles covering as much of the southeast and southwest slopes of the roof as was possible.
U value: 0.056 W/m2K
Roof (extension)
The flat-roofed extension had a major overhaul. The flat roof was replaced with an insulated pitched roof (mineral wool between timber members and phenolic foam insulation board), designed and angled to maximise installation of solar PV panels.
U-Value: 0.086 W/m2K
Flood-resilient ground floor
The house is near the bottom of a hill, with water flowing underground and rising close to the surface after heavy rainfall. Laurie wanted to achieve a U-value below 0.1 which meant having at least 200mm of low-lambda insulation, extending below the highest water levels seen in recent months and potentially creating a buoyancy problem. He also wanted the house to be future climate-resilient, bearing in mind that Oxford could experience three or more times the historical rainfall record. Careful thought went into a ground floor design so that it could cope with water pressure from below. A ground-bearing concrete structure would have been the obvious option, but Laurie wanted to avoid using concrete because of the 2 tonnes of embodied CO2 it would have implied. He ended up specifying a timber floor with joists resting on insulation and fixed to the walls to withstand upward loads. The original structural engineers working on the project were not prepared to agree to a floor other than suspended timber or ground-bearing concrete (for which British Standards exist). Laurie carried out the structural and thermal calculations to show that the structure would meet Building Regulations requirements at least as well as a conventional floor. Eventually, a structural engineer was found who was willing to provide the final specifications for the joists and fixings. The building control officer was very enthusiastic, calling it a ‘warm raft’ floor.
The floor make-up comprises:
- Pine floorboards
- 150mm timber joists fixed to wall plates, bolted to the walls with bonded anchor rods. The floor void is filled with DriTherm 32 mineral wool
- Breathable airtight membrane
- 18mm OSB to spread the load over the insulation
- 225mm PIR board
- DPM
- Sand
- Hardcore
U-Value: 0.072 W/m2K
Party wall
Wood fibre internal wall insulation from NBT was used on the party walls between the neighbouring house to eliminate thermal bridges and reduce noise.
Heating
An air-to-air heat pump is used to heat the house, which can also act, if needed, as an air conditioning unit in the summer. The overheating strategy at the project is still being developed, so having the possibility of air conditioning is a precaution.
MVHR heat recovery ventilation
21° designed, supplied and commissioned the MVHR system at the project. A Paul Focus 200 MVHR unit was used, with galvanised steel ducting. Some of the MVHR ducting had to run through rooms and so is boxed in. The MVHR unit is located in a downstairs plant room along with batteries and equipment for the solar PV system
Laurie Michaelis - Client
Triple glazed windows and doors
PROGRESSION triple glazed timber windows, with external Thermowood cladding and a whole window U value of 0.68 W/m2K, were specified for the project. The windows were finished in a dark grey stain on the outside, nature effect on the inside. The entrance doors were from the ULTRA triple glazed timber range. Door styles included GRO3 and fully-glazed GLO1, finished in RAL 7016 paint finish on the outside and nature effect on the inside.
The windows were all installed in plywood boxes, with the window frames located within the insulation zone. The external wall insulation overlaps the window frames to minimize thermal bridging. Green Building Store supplied Psi values for the window installation detailing.
The windows and doors were specified by the architect and approved by Laurie because of their low U values.
Laurie Michaelis - Client
Working with 21°
Laurie was already familiar with 21°, knowing Chayley Collis and Chris Herring from Quaker climate events and gatherings.
Laurie Michaelis - Client
More information - Listing on Passive house database
Project details
Architect
Builder
Passivhaus certifier
Completed
2020
Case study
2021